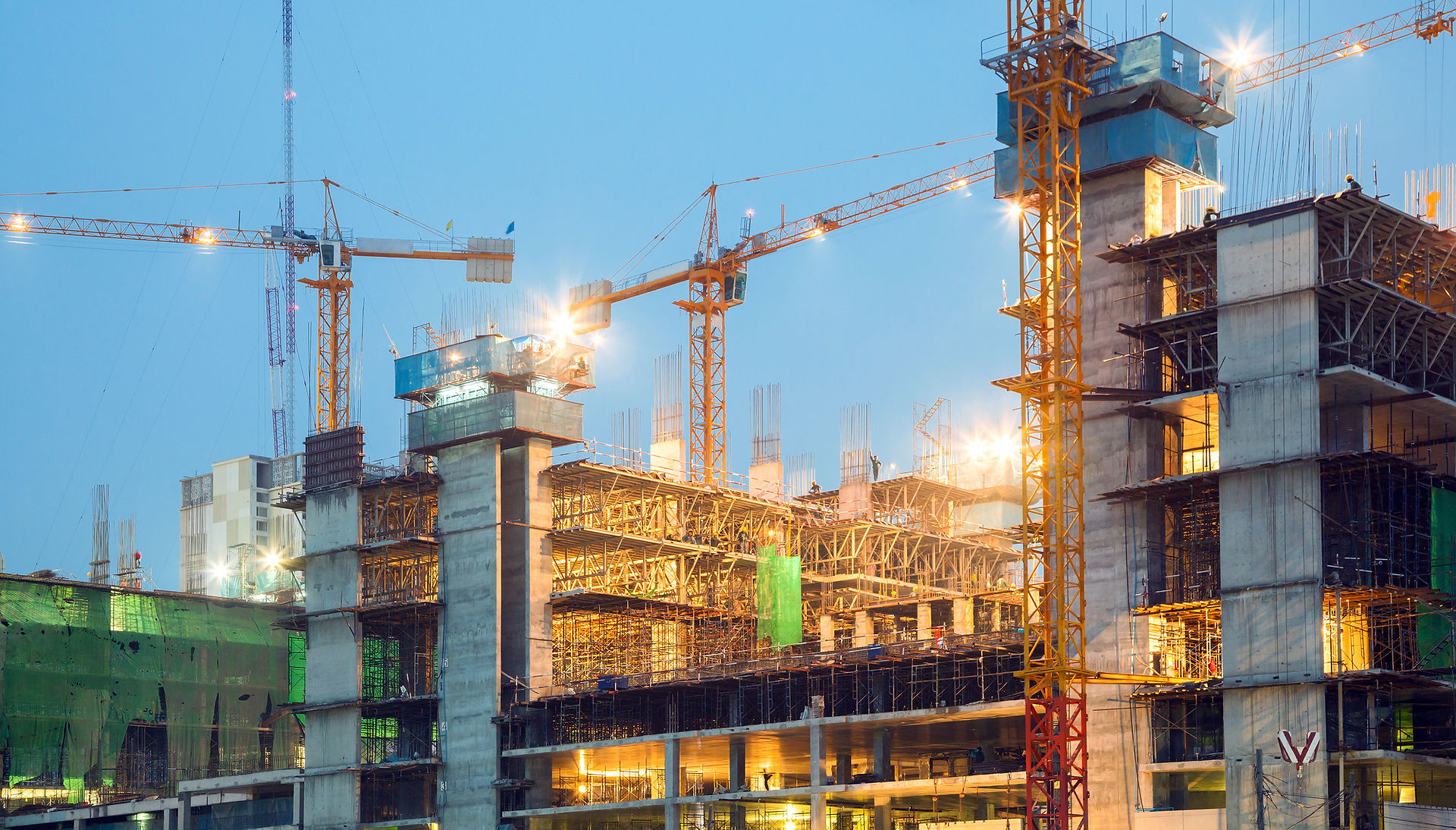
Summary
The RC will be built in phases. Since most parts are already in the hands of the manufacturers, a good amount of assembly can be done already right off the bat. The biggest part will be the chassis since it wields every other part that is a component of the RC. Once that is complete, the a-arms, drive shaft, wheel hub assembly and camber arms will be added. Holding off mounting the wheels will allow for more space and versatility to mount all the electronics so the wheels and tires will be mounted last. Next will be the steering servo because it is the most complex component to place and get right. After that, the rest of mostly plug and play as far as electronics go. Some weight balancing will need to be performed to reduce having too much force applied to one side during the drop test. The car will be 2wd meaning the motor is going to be in the rear of the car focusing most of the weight to the back.
Differential Housing
The first part being constructed is the differential, the main focus. The design was remastered to include a more educated clearance fit for the top cover of the enclosed gear box. To make this part, use of a 3D printer is in order utilizing left over material in spools that the lab already has. Preferably, PLA plastic would be used for printing because of its more ductile qualities as opposed to ABS which has much more brittle qualities. After the printing of the differential housing and top cover, the machine shop will be used to create countersinks, chamfers, and to clean out holes with a reamer if needed. For the top cover, each hole that is aligned for the screws will need to have counter sinks because of the shape of the screw head. Threading the holes for the specific screw being used will be attempted; however, since it is difficult to calculate how the material will react, it may be just as productive to pilot them in. After the holes are finished for the screws, a test fit must be made for the pins holding the gears. These holes must allow the pin to be fully inserted when the top cover is seated on the housing. If this is not the case, the problem will have to be fixed by either altering slightly in the machine shop or reprinting one or the other. This will be the only part that is being printed since most of the other parts are gears and will be purchased. There will be a secondary option for the gears since they were created in solid works and this is to resin cast them. There was little to no analysis done for this because it was determined that they would shear at the lowest amount of torque required for the car to take off at a moderate pace.
Differential Construction/Functionality
Design Progress/Timeline

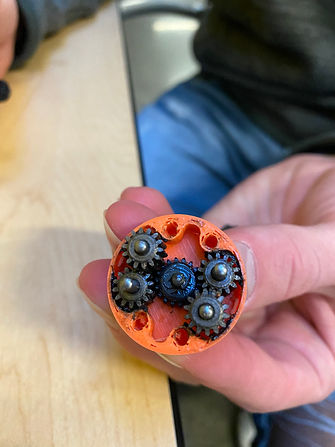



