
SCHEDULE
​
DESIGN
The design portion of this project occurs during the Fall quarter of the academic year and looks to complete three major components. These components include the work and completion of a proposal, analyses constituting 12 computational engineering sheets that employ RADD techniques, as well as designing, modeling, and ANSI Y14.5 detail drawing project components.
The twelve computational green sheets are submitted weekly throughout the quarter and require the student to define a problem, present a solution, define a requirement, analyze the situation, and yield a design parameter from said analysis. Finally, the student then incorporates said parameter into the design of a component and produces a detail drawing of the component based of ANSI Y14.5 standards. These analyses and drawings are then incorporated into a proposal.
​
​
CONSTRUCTION
​
The construction portion of this project occurs during the Winter quarter of the academic year and looks to complete the manufacturing of all the student-designed parts for the RC Baja project. All manufacturing is completed by the students. Due to the effects of the COVID-19 pandemic, MET faculty intervention is at times required to aid in efforts such as 3D printing qualifying parts. The purchase and acquisition of non-student designed parts that are necessary for the operation of the RC Baja vehicle also occur in this portion of the project.
Part inspection, compatibility testing, and practicality evaluation also occur in this portion of the project. After a part is manufactured, the NRJ RC Baja team will inspect the part and test its compatibility with other parts of the various RC assemblies and discern whether or not the part successfully serves its function. If any issues arise, revisions and redesigns will be instituted. Thus, multiple builds of a single part may occur in order to optimize the part’s function and design.
The end of this portion of the project will yield a fully functional RC Baja vehicle ready to move on to the testing portion of the project.
​
​
TESTING
​
The testing portion of this project occurs during the Spring quarter of the academic year and looks to complete the testing and evaluation of the student-designed and student-manufactured parts for the RC Baja Project and the complete RC itself. The requirements defined for each component, assembly, or system are to be evaluated.
The systems to be tested are the suspension and transmission systems. The three main tests that will occur in this phase are an assembly and disassembly test for the transmission cover, an operation test for all the RC components together, and a loading test for the suspension tower.
The tests results will then be documented, analyzed, and discussed. The testing page of this website and the testing report in the project report contain the relevant information.
​
​
GANT CHART
Please see below the updated Gant Chart being used for the design portion of this project:
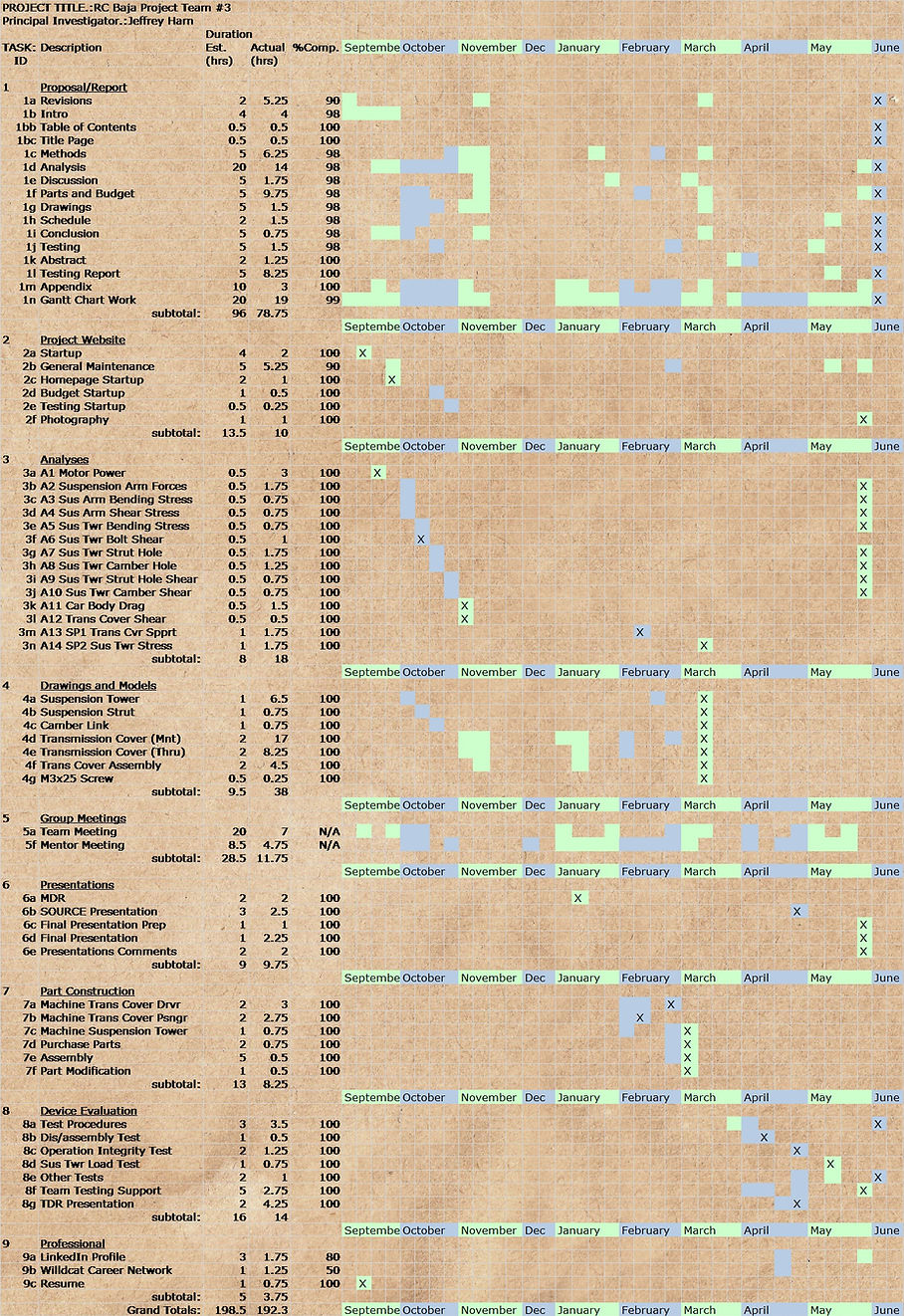
BUDGET
​
OVERALL ESTIMATED COST
Currently, the entire project estimated cost is set at $350. This is broken down into three different budgets, as follows. A fund of $200 is planned for the expenses of purchased RC electrical components and parts. A fund of $100 is planned for the cost of materials, namely, the cost of wood for the chassis and the cost of 3D printing polymer material. An emergency fund of $50 is budgeted. Both the $200 and $100 budgets are overestimated so as to provide a contingency cushion if problems arrive. Please see the below budget table for more specific details. The budget below is still under work.
​
​
BUDGET TABLE
Please see below the updated budget table for this project:
​
